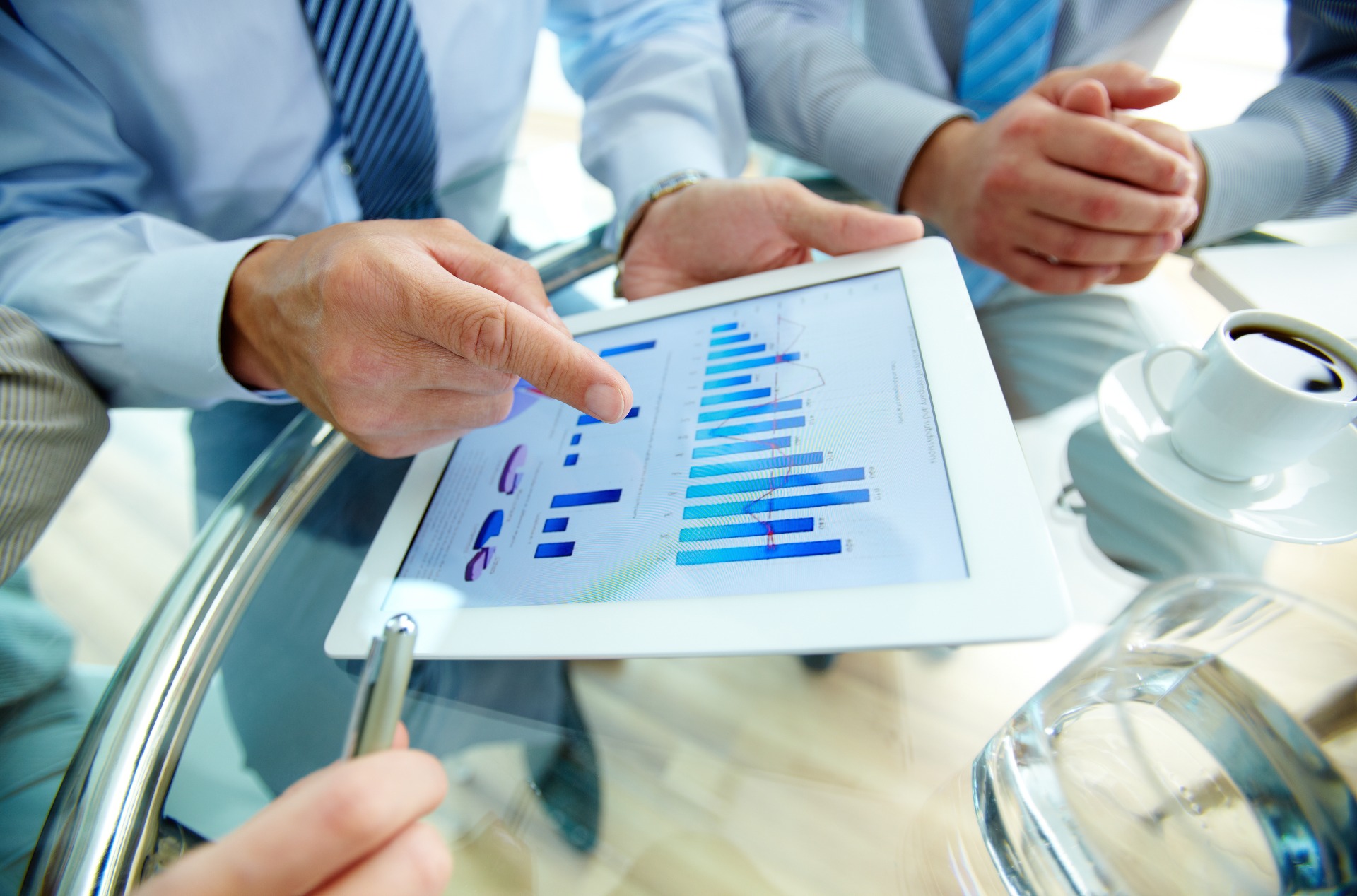
OUR RESULTS
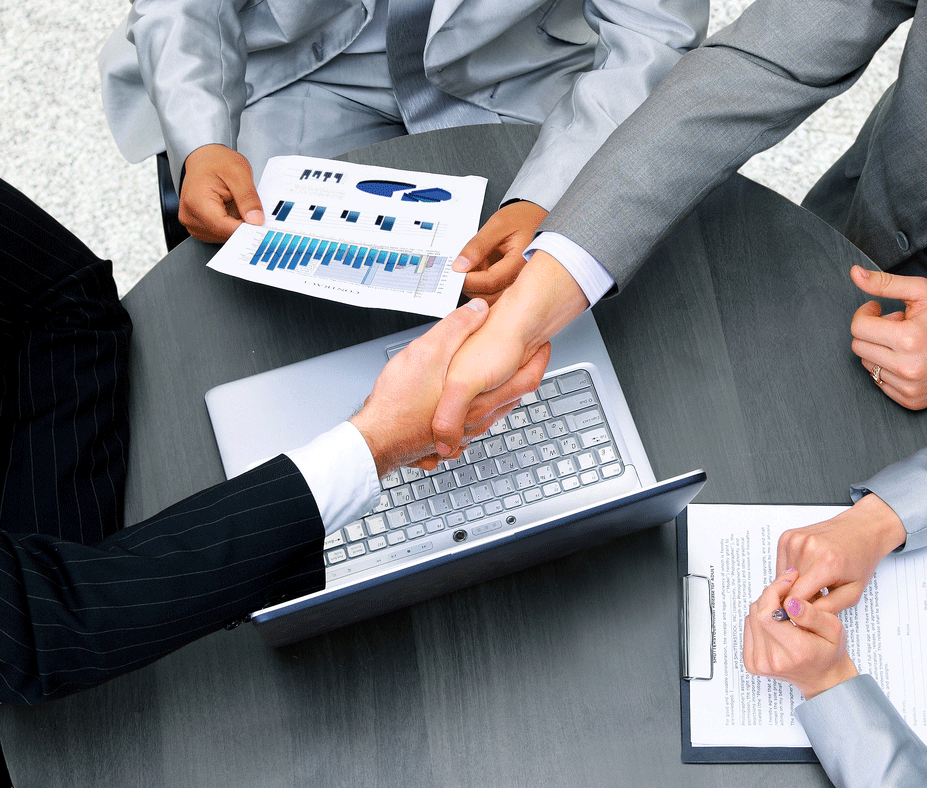
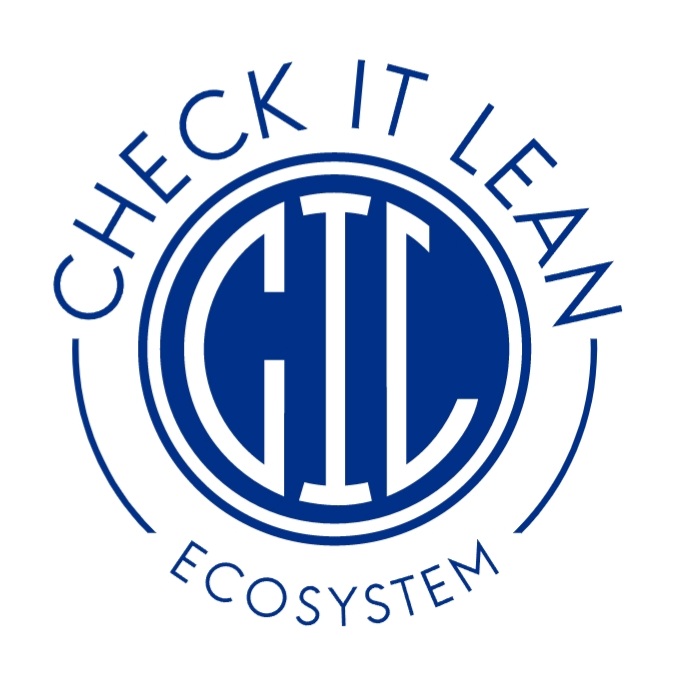
OUR RESULTS
1/ CNC Machining production plant optimization:
As a result of the developed and implemented production optimization, the amount of work performed and internal production increased by 25% in addition to the improvement of quality indicators. Original effectiveness 44%, after development and optimization 69%, all within 5 months.
2/ Welding and CNC machining production plant design, process planning:
Starting with layout design, load testing, material flow planning, planning the number and design of workplaces, determining the number of employees and production equipment, creating workstations and production lines, making proposals for the design and purchase of new production equipment up to mass production. The duration of the project is 4 months.
3/ Cooperative production optimization and reasonable cost reduction:
The level of cooperation was reduced to 20% from the original 43% by optimizing internal production capacity utilization, reasonable production planning, and the possibility of product and operation combinations. The duration of the project is 2 months.
4/ CNC machining tool cost reduction:
Tool costs were reduced by 35% with the introduction of the introduced and applied tool cooling technology and supplier changes. By installing an automatic tool and setting a minimum stock level. The duration of the project is 2 months.
5/ Production line design and installation, planning and production optimization of I- and U-cells:
Production line cycle time measurements, equalization. Reasonable operation mergers and staff optimization. Result Production of 10-25% more products per shift. The duration of the project is 6 months.
6/ Production line installation, adjustment, test production, process development all according to the Lean methodology:
We installed production lines for the Customer by the Supplier and prepared them for mass production. We have completed the necessary test productions. We developed the production, maintenance and quality assurance documentation system for the production lines. Together with the Supplier and the Customer, we performed a qualifying production line audit, then handed over the production lines to the production department for serial production. Project duration: 9 months.
7/ Muda reduction and elimination:
Conducting employee training (Training). Development of a documentation system. Definition of a pilot production area. Production Line "Loss Hunting" Conducting Audits. Introduction and then Follow-up.
Result: After mapping and eliminating the losses, the efficiency of the production line improved by 5-8%. The number and duration of machine stoppages and line micro-stops decreased by 3-5%.
Additional results: We eliminated production line and technology losses (7+1 MUDA). We standardized the production processes (e.g. material flow, changeover). We have reduced Employee errors and the possibility of deception (e.g. PokaYoke). We have made production processes safer. Production outputs have become more predictable. The duration of the project is 3-6 months.
8/ Obeya Room and Shop Floor Management (SFM):
Obeya is a LEAN concept that helps generate ideas, brings decision makers together to execute the PDCA cycle and quickly develop solutions. Obeya focuses on improving communication and increasing efficiency, the place where the PDCA cycle is physically mapped. Obeya Room and as part of it Shop Floor Management is a Management tool for monitoring production results, tracking production KPIs, recording problems hindering production processes and initiating and following up the resolution of problems. The duration of the project is 3-6 months.
9/ Employee Ideation/Innovation System development:
Documentation system, Process description, Process map preparation. Completion of trainings. Introduction. Operation. The duration of the project is 3 months.
10/ Other results:
10.1/ Assembly rear bumper production reconstruction (6 months). Savings of €407,000 with the new layout.
10.2/ Assembly plant scrap reduction 477,000 € (2019.12-2020.02), 218,000 € (2020.03-2020.05). Result: -55%/3 months.
10.3/ Injection molding plant layout optimization, development of the useful production area (22 machines, 3 months). Result: +500 m2.
10.4/ Injection molding plant workforce savings (MTM) (continuous measurement). Result: -22 people. -1,750,000 €/month.
10.5/ Storage area release (3 months). Result: from 5,785 m2 to 4,000 m2. -1785 m2, -31%.
10.6/ Production optimization, internal production efficiency improvement (OEE) (3 months). Result: from 42% to 67%. +25%.
10.7/ Production optimization, full-scale design of an acid-resistant parts production plant (6 months). Result: +2,000 m2.
10.8/ Carbon steel welding plant layout area savings for new production (3 month). Result: -300 m2. -7.3%.
10.9/ Carbon steel welding plant production process acceleration (1 month). Result: +1.5 products/shift. +19%.
10.10/ Six Sigma project (6 months): Production optimization. Result: Annual cost savings: €15,000.
10.11/ SMED on CNC machining centers with hydraulic tool clamping (3 months). Result: -85%.
10.12/ Development of a TPM Maintenance System. Design, implementation, and maintenance of a full-scale Effective Maintenance System. (9-12 months).
If you are interested, we are at your service.
Ask for our quotation through the Contact page!
CHECK IT LEAN - Engineering Solutions